Industrial Magnetics, Inc.
TRANSPORTER®
The Low Profile Transporter® LP magnetically transfers metal blanks, stampings and parts in automated station to station, press-to-press transfer and robotic pick and place systems. Typical applications include stamped parts, tailor welded blanks, body panels and refrigerator door panels.
-
Uses up to 95% less air than vacuum cups
-
Grasps odd shaped or perforated parts
-
Operates effectively in any orientation
-
Outlasts most vacuum cups
-
Positively holds parts - no dropping or shifting
-
Threads onto typical 3/8 NPT vacuum cup tooling
-
Operates on 25 to 60 psi shop air
-
Approximate weight 0.75 Lbs.
-
Durable design for long maintenance free operation
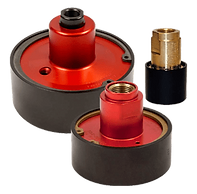

TRANSPORTER® MAGVAC
From the platform of its most successful product ever, IMI introduces a new product to the Transporter® Family, the Transporter® MagVac- a combination of magnetic and vacuum technology.
Like the Transporter® and Transporter® LP - magnetic tooling designed for lifting and holding ferrous steel in stamping, blanking, press-to-press transfer and related applications – the Transporter® MagVac is next-generation technology.
The difference is the incorporation of vacuum technology, which makes the Transporter MagVac the most universal End-Of-Arm-Tooling available. With part-holding values higher than traditional vacuum- and more efficient and accurate than vacuum or grippers- the Transporter® MagVac is the solution that eliminates tool-changeover and costly downtime.
The Transporter® MagVac will lift and hold all shapes and types of steel- from brass and aluminum to ferrous and stainless, perforated, oily or painted. The integrated and patented magnet/vacuum design is million-cycle tested for endurance. When in use on ferrous steel, it incorporates a Fail-Safe feature so that in the event of air loss, parts will not release.
-
No more replacing vacuum cups every week
-
No more parts slippage and die damage due to part misplacement
-
No more dropping parts when there is a loss of shop air
-
No more dropping parts because of excess mill oil or weld slag
-
No more tooling change and downtime when a new part shape is in the process stream
